Can you tell us about the level of plastic waste being discharged into the world’s oceans?
Since the 1950s, human beings have generated an estimated 6.3 billion tonnes of plastic waste. However, only 9 per cent of this waste has been recycled and 12 per cent burnt in incinerators. The remaining 79 per cent has been dumped, and much of it has ended up in the oceans.
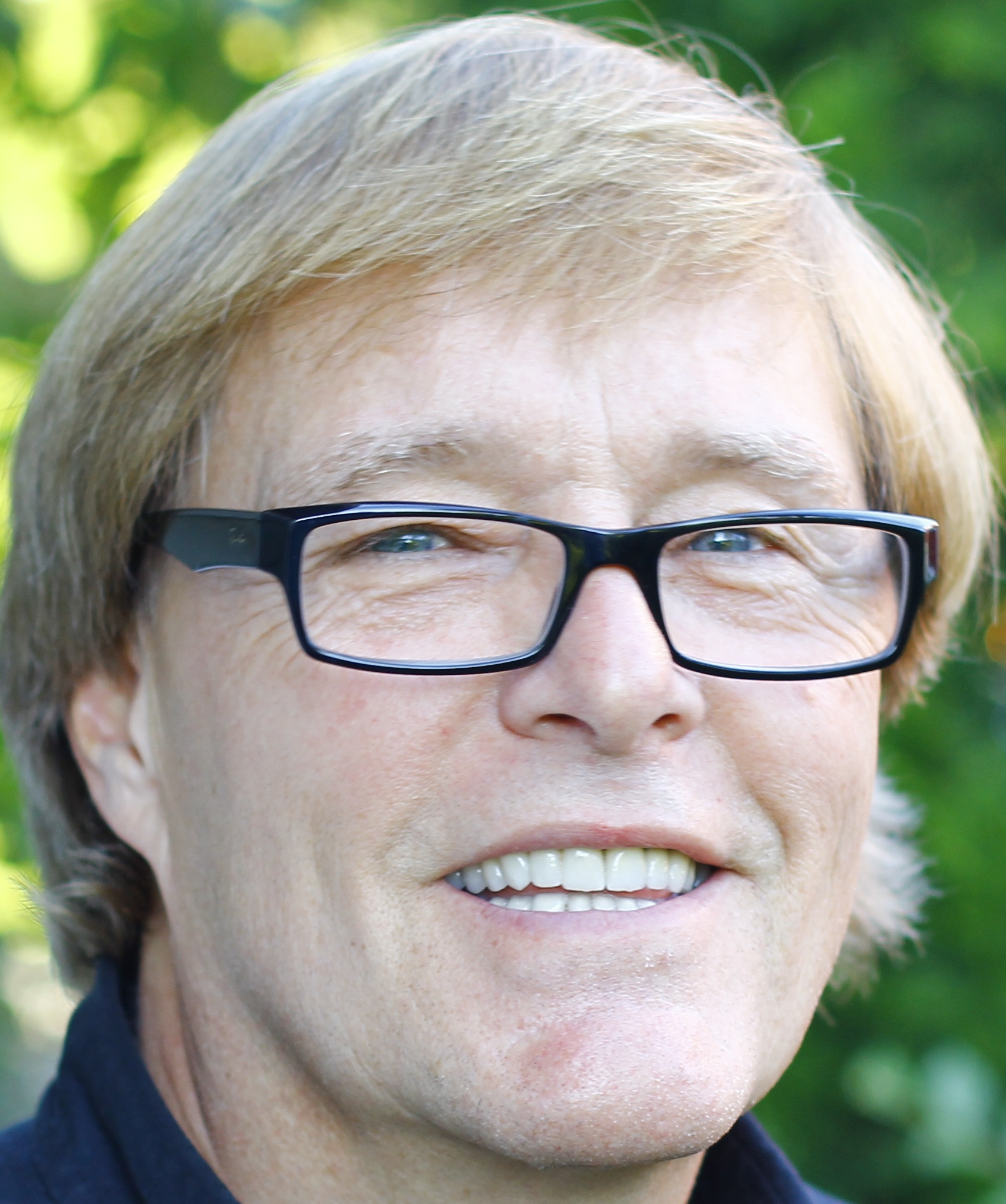
According to international studies, Vietnam is responsible for some of the highest levels of plastic discharge into the world’s oceans. The combination of an elongated coastline, the growing use of plastics, and an inadequate waste management infrastructure all mean that the country discharges between 73,000 and 280,000 tonnes of plastic waste into the oceans every year.
Most of the plastic that reaches the oceans is non-recyclable in nature. According to recent studies, even if we continue to develop effective waste collection and recycling systems, there will still be large volumes of plastics that cannot be recycled.
As Vietnam is aiming to build a circular economy and tackle the serious “white pollution”, turning plastic waste into resources for utilization in resource and energy-intensive industries is seen as one of the feasible solutions.
What is the potential solution for Vietnam?
Using non-recyclable plastic waste as an alternative and substitute for coal in cement production may prevent huge volumes of plastic from being discarded into the oceans and will also reduce CO2 emissions. SINTEF, one of the largest independent research organizations in Europe, has been working on these aspects in Asia since 2019 under its regional project called Ocean Plastic Turned into an Opportunity in Circular Economy (OPTOCE), which is funded by the Norwegian Agency for Development Cooperation (Norad). Under the project, a successful pilot demonstration was conducted at the INSEE Hon Chong cement factory in the Mekong Delta’s Kien Giang province in December 2021 to assess the feasibility of using non-recyclable plastic waste from Vietnam’s largest paper recycling plant and rubber waste from shoe/footwear manufacturing as co-fuels.
Cement production requires massive volumes of coal and other raw materials. However, all of these components can be substituted in cement kilns, either entirely or in part, by waste that contains energy and/or inorganic components. The substitution process is called co-processing or integrated waste management.
This approach has been shown to be cost-effective, resource-efficient, and environmentally-friendly when compared to combustion in an incinerator. The energy efficiency is much higher than in modern incinerators that generate energy from waste. Nor are any residual products generated, compared with about 30 per cent by volume in a traditional incinerator.
In Europe, co-processing is already an important pillar for sustainability in the cement industry, and cement plants in Norway are substituting as much as 80 per cent of their fossil fuels such as coal and oil with several types of waste, including non-recyclable plastic waste. In Asia, this substitution rate is still only 3 per cent on average. Co-processing of waste such as non-recyclable plastic waste is not yet common in Vietnam’s cement industry. Only a handful of cement plants are currently co-processing waste in the country.
The pilot demonstration at INSEE Hon Chong concluded that local co-processing of non-recyclable plastic waste as a fuel substitute in cement kilns is a feasible alternative, both environmentally and technically. The tests demonstrated that the emissions of dioxins did not increase if plastic waste is used as a supplementary fuel, and they complied with the strictest international limit values.
What is the lesson learned from INSEE Hon Chong?
Vietnam has the fifth-largest cement industry in the world. Lessons from the successful trial at INSEE Hon Chong can be replicated in other cement clusters, especially in the country’s north. The cement industry has a Thermal Substitution Rate (TSR) of <1 per cent and, therefore, co-processing can play an important role in integrated waste management, reducing the need for high investments in conventional WtE (Waste-to-Energy) incinerators. It is estimated that by achieving a TSR of 13 per cent, all of Vietnam’s plastic waste could be treated in cement plants.
Cement companies need to see the potential of becoming an actor in low-quality and non-recyclable plastic waste management, and through this, contribute to reducing the flow of plastic waste into our oceans.
SINTEF is one of the largest independent research organizations in Europe and has been conducting the regional OPTOCE project since 2019, which is funded by Norad and part of the Norwegian Development Program to Combat Marine Litter and Microplastics, launched in 2018.
OPTOCE aims to showcase how the cement industry can be involved and increase the treatment capacity for Non-Recyclable Plastic Wastes in China, India, Myanmar, Thailand, and Vietnam, thereby contributing to reducing the release of plastics into the seas.
In Vietnam, OPTOCE entered into an agreement with Vietnam’s largest paper producer, which is located in the Mekong Delta and produces large quantities of non-recyclable plastics waste, such as pieces of tape, laminated plastic pieces, and stickers.
In December 2021, a successful pilot demonstration was conducted in the INSEE Hon Chong cement plant to assess the feasibility of using non-recyclable plastic waste from the paper producer and rubber waste from shoe/footwear manufacturing as co-fuels. The valuable lessons can be shared with the other cement plants for replication and scale-up.
SINTEF will organize a workshop with the Vietnamese Cement Association on September 29 and call for participation from more cement plants in Vietnam.